How the heck can I get THIS out???
#1
#2
You could try to tack-weld a small 1/4 or 3/8" extention on the end of the head or try to weld an Allen key on there . . .
IMO you shouldn't have used an impact, when I redid my seals (LINK)I used a small 1/4" drive 6" ratchet to remove that little thing and it wasn't very hard.
My idea will seem retarded what I'm sure most of the guys here have
**EDIT - that bolt should have been a 5/16" initially
IMO you shouldn't have used an impact, when I redid my seals (LINK)I used a small 1/4" drive 6" ratchet to remove that little thing and it wasn't very hard.
My idea will seem retarded what I'm sure most of the guys here have

**EDIT - that bolt should have been a 5/16" initially
#3
That's just it. I couldn't budge it with a 6" 1/4 drive ratchet, nor a 3/8's drive 12" ratchet with an adapter. So the next best thing was an impact on low torque/pressure with a swivel (universal) adapter.
I considered tack welding a socket onto it, but never an extension onto the end of the bolt head! Good thinking!
I considered tack welding a socket onto it, but never an extension onto the end of the bolt head! Good thinking!
#5
*do not tack weld* Doing that can cause the pinion and ring to arc.. or arcing within the bearings. That is if you plan on keeping them..
Using a small grinder (like a dremel tool) Cut two flats on the flange of the head. And the distance between them being a snug fit to an appropriate sized open end wrench. Then using that dremel tool clean up the hex shape and hammer on another socket that will fit.
Between the two you'll have doubled your contacting surafaces of the wrenches. That way you'll stand a better chance of turning it.
Rich
Using a small grinder (like a dremel tool) Cut two flats on the flange of the head. And the distance between them being a snug fit to an appropriate sized open end wrench. Then using that dremel tool clean up the hex shape and hammer on another socket that will fit.
Between the two you'll have doubled your contacting surafaces of the wrenches. That way you'll stand a better chance of turning it.
Rich
#9
Join Date: Jul 2006
Location: Nokomis, FL / Tallahassee
Posts: 784
Likes: 0
Received 0 Likes
on
0 Posts
#11
Unregistered User
Posts: n/a
first thing is you answered your own question, why are you using a impact gun ?????
now your somewhat screwed.
you will need to get something to bite the head(whats left of it) and use a mapp gas hand held torch and head the carrier up just enough the break the loc-tite loose and try to turn the bolt.
a little heat wont hurt it, you could even get that area red hot if you want to.
now your somewhat screwed.
you will need to get something to bite the head(whats left of it) and use a mapp gas hand held torch and head the carrier up just enough the break the loc-tite loose and try to turn the bolt.
a little heat wont hurt it, you could even get that area red hot if you want to.
#12
yea, I'd suggest heading the head of the bolt with either a MAPP or even a propane torch as locktite is definitly used from the factory on that pin, then maybe try a set of needle nose vice grips on it and get it to break loose. Once it breaks the locktite loose it should spin right out no problem which is what the heat is for, and yes you can get that bolt good and warmed up just be careful nothing in there lights on fire...
IF you cant manage to get it out at all, you can grab a large punch and a BIG hammer and actually hammer the crossshaft out of the carrier snapping the retaining bolt at which point you would at least be able to pull the axleshafts and pull the carrier out to either work on it on a bench somewhere or just get another open carrier for a 7.5 for about $5 bucks and setup the ring gear on the new carrier.
IF you cant manage to get it out at all, you can grab a large punch and a BIG hammer and actually hammer the crossshaft out of the carrier snapping the retaining bolt at which point you would at least be able to pull the axleshafts and pull the carrier out to either work on it on a bench somewhere or just get another open carrier for a 7.5 for about $5 bucks and setup the ring gear on the new carrier.
#13
get some of those robo grip pliers they proly wont get it out but it will do a great job tearin it the rest of the way up. i hate those things
no but really a lil heat should do it an also the threads on that are bout 3/8 long and they start right at the head so you just got to heat a lil spot
no but really a lil heat should do it an also the threads on that are bout 3/8 long and they start right at the head so you just got to heat a lil spot
#14
I would try a little heat on the bolt head. Just enough to soften up any loctite that might have been used. Then tap the head with a cold punch a few times. The next thing is to find the next size smaller socket, metric or SAE, that’s close to fitting it and tap it on. Once you have it on…try tightening the bold just a little first, then unscrew it. If that doesn’t work, try what FMD suggested or if you dont want to spend the bucks for the tools try a cold chisel and tapping the side of the head to unscrew it.
#15
I now have the perfect method for removing stripped bolts.
Follow this procedure:
Ha ha...I got so lucky today! That Matco tool guy was a God-send.
He let me borrow a set of bolt extractors and with a little blow torch and hand-cranking it came right out.
CHECK OUT THIS DAMAGE!!!

The rest of the removal was a piece of cake!
Slide the pinion shaft out of the way of the axle shafts.

Push each axleshaft inwards to allow access to the U-clip. Remove U-clip from the end of the axleshaft with a pair of needle-nose pliars.

Lift out rotating assembly. Make sure to set aside the bearing race from each end.
If re-gearing, remove the 10 ring gear bolts.

Make sure to have lots of newspaper or cardboard to lay the greasy stuff on. I have never in my life seen so much grease!

Would there be any use in making a "How-To Re-gear" thread using these and other pictures I took?
Follow this procedure:
- Beat the heck out of it for 2 days, then give up.
- Take another look, then get REAL lucky and have the Matco tool guy DRIVE THROUGH YOUR NEIGHBORHOOD just as you're about to give up again.
- Run like mad, waving your arms like a monkey, and chase down the Matco Tool guy like he's got a truckload of free ice cream
- Allow him to grace you with his presence and almighty tool collection
- Remove bolt effortlessly
- Be happy, drink lots of water.
Ha ha...I got so lucky today! That Matco tool guy was a God-send.
He let me borrow a set of bolt extractors and with a little blow torch and hand-cranking it came right out.
CHECK OUT THIS DAMAGE!!!

The rest of the removal was a piece of cake!
Slide the pinion shaft out of the way of the axle shafts.

Push each axleshaft inwards to allow access to the U-clip. Remove U-clip from the end of the axleshaft with a pair of needle-nose pliars.

Lift out rotating assembly. Make sure to set aside the bearing race from each end.
If re-gearing, remove the 10 ring gear bolts.

Make sure to have lots of newspaper or cardboard to lay the greasy stuff on. I have never in my life seen so much grease!

Would there be any use in making a "How-To Re-gear" thread using these and other pictures I took?
#17
Originally Posted by Needforspeed3685
Slide the pinion shaft out of the way of the axle shafts.
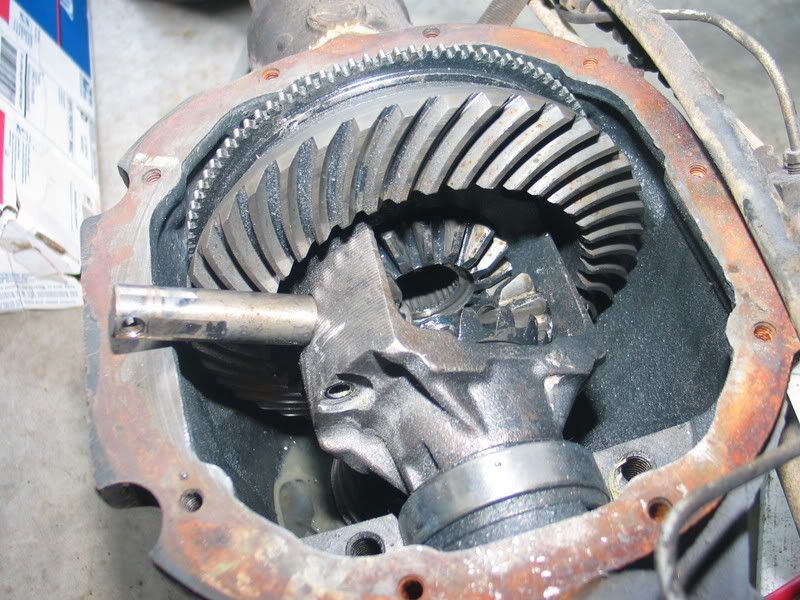
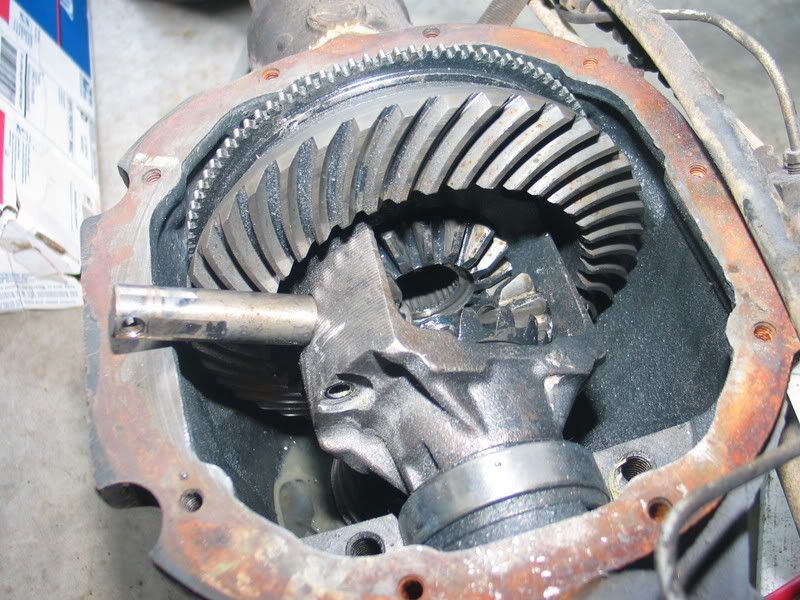
I wish I would have saw this months ago, I have an explorer axle sitting in my garage that i pushed the pin almost all the way out, but I Didnt rotate it, and its stuck inside the diff now, and its too damn greasy to pull it out
#18
Originally Posted by ScottG
I wish I would have saw this months ago, I have an explorer axle sitting in my garage that i pushed the pin almost all the way out, but I Didnt rotate it, and its stuck inside the diff now, and its too damn greasy to pull it out
#19
#22
Originally Posted by TireIron
I hope you marked which side and what orientation the bearing caps came from as they are machined to the housing and must be replaced in the exact position they came out of...
#23
#24
Originally Posted by Needforspeed3685
Yes I did label them, although I won't be using this rear end. I'm trying to part it out or get rid of the whole thing.
Oh and for parting out, keep in mind that the axleshafts are identical between the 7.5 and the 28-spline 8.8 so it gives you a much larger base of people looking for parts.
#25
Originally Posted by Needforspeed3685
I now have the perfect method for removing stripped bolts.
Follow this procedure:
Ha ha...I got so lucky today! That Matco tool guy was a God-send.
He let me borrow a set of bolt extractors and with a little blow torch and hand-cranking it came right out.
Follow this procedure:
- Beat the heck out of it for 2 days, then give up.
- Take another look, then get REAL lucky and have the Matco tool guy DRIVE THROUGH YOUR NEIGHBORHOOD just as you're about to give up again.
- Run like mad, waving your arms like a monkey, and chase down the Matco Tool guy like he's got a truckload of free ice cream
- Allow him to grace you with his presence and almighty tool collection
- Remove bolt effortlessly
- Be happy, drink lots of water.
Ha ha...I got so lucky today! That Matco tool guy was a God-send.
He let me borrow a set of bolt extractors and with a little blow torch and hand-cranking it came right out.

Thread
Thread Starter
Forum
Replies
Last Post